Modernizing Your Warehouse: Creating a Modern Warehouse
- imaddbox
- Dec 19, 2022
- 4 min read
Updated: Jul 6, 2024
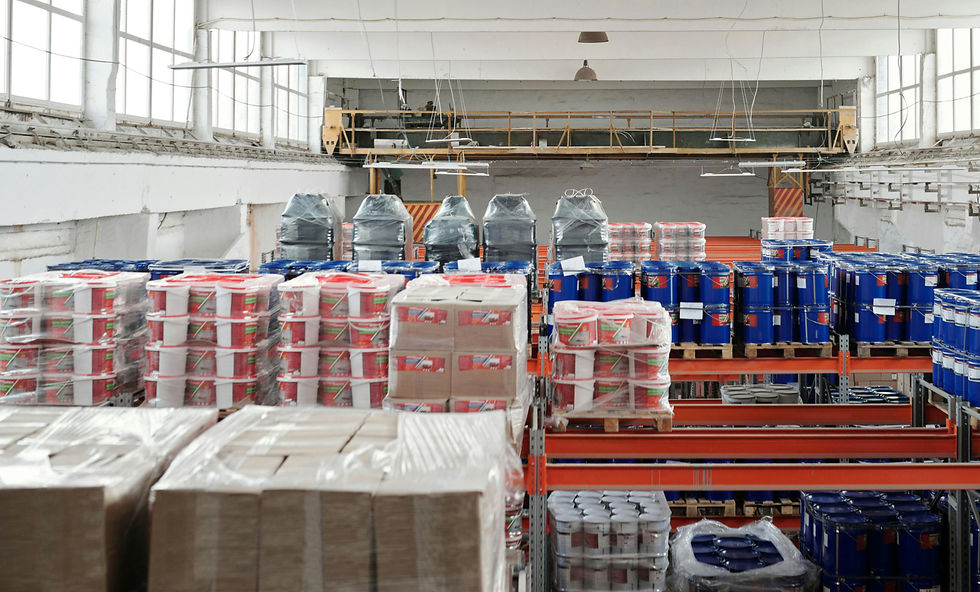
This is Part 5 of a five-part series for midmarket distributors looking to bring their warehouses into the 21st century and beyond. If you haven’t already, we recommend you start with Part 1.
WAREHOUSE TECHNOLOGIES AND CONSIDERATIONS
Managing inventory and warehouse operations is easy when you are small. Warehouse management becomes more difficult as distributors grow, adding more locations, large facilities, and larger product lines.
Growing distributors and those using entry-level accounting or legacy distribution ERP systems must modernize warehouse operations to remain competitive. This often warrants a replacement of the business system or the acquisition of expensive warehouse management software.
This series of articles provides wholesale distributors with an overview of warehouse management features and technologies. It includes a self-assessment to determine what steps to take next. It also provides WMS strategies and a process for executing WMS implementations to modernize warehouse and distribution center operations.
CREATING A MODERN WAREHOUSE
It is time to execute the modernization project once you have defined your plan. Remember that you do not have to automate everything at one time. Break down the project into smaller activities. Execution covers four phases: preparation, go-live, review, and continuous improvement. Each phase is essential for the successful roll-out of new warehouse strategies.
PHASE ONE: PREPARATION
The time it takes to prepare will depend on the project’s complexity, including the technologies used and the scope of changes. Preparation should start well in advance of your desired go-live date. It should include a review of the project plan with project owners, internal staff, users, and technology providers.
1. Plan Review: Review the implementation plan with the team. Set the start date for the project and assign dates to each step in the project. Consider the contingency plan to ensure there is a process in case something goes wrong.
2. Team Preparation: Notify participants of timelines and their roles and responsibilities. A conference room pilot (CRP) improves success rates dramatically.
PHASE TWO: GO-LIVE DAY
Successful go-lives are well-organized. Identify one person as the project lead. The project lead orchestrates each step in the project.
1. Coordination: The project lead orchestrates the implementation. They delegate tasks to team members and guide the entire project. They make decisions based on feedback and chart progress throughout the process.
2. Documentation: The actual go-live should be as close as possible to the planned implementation. Last-minute changes inevitably happen along the way. Document changes with details for future review.
PHASE THREE: REVIEW
It will take time for things to settle into place after you complete the project. Give users time to adapt to new processes while providing time to collect data.
1. Go-Live Notes: Review the go-live notes for last-minute changes to the project plan. Identify if there are any follow-up activities to fine-tune the process.
2. User Feedback: Talk to users about new processes and technologies. What do they like? What do they dislike? Do they feel they are beneficial? You will find that users have some of the best ideas if you take the time to ask them.
3. Analytics: Review the early results. Were you able to meet or to exceed your goals? If not, why? What can you do to improve the process?
PHASE FOUR: CONTINUOUS IMPROVEMENT
Application upgrades and other issues impact the original project. New versions of the software or hardware can provide increased value.
1. Maintain Technologies: Stay current on the latest updates of your ERP software and connected technologies. Set up a sandbox for testing upgrades. Review product road maps and understand technology lifecycles.
2. Improve Processes: Look for ways to use existing features and technologies to further improve processes and automation.
3. Explore New Opportunities: Look for new ways to extend your modernization projects to other transactions or business processes. Take on more complex projects and consider more advanced technologies down the road.
WHAT ACUMATICA CAN DO FOR YOU
Acumatica Cloud ERP provides the best business management solution for digitally resilient companies. Built for mobile and telework scenarios and easily integrated with the collaboration tools of your choice, Acumatica delivers flexibility, efficiency, and continuity of operations to growing small and midmarket organizations.
MODERN WAREHOUSE MANAGEMENT WITH ACUMATICA DISTRIBUTION EDITION
A modern warehouse is crucial for wholesale distributors to thrive in today’s digital economy. Entry-level business applications and legacy ERP software pose barriers to modernization projects forcing many distributors to invest in costly customizations or complex and expensive warehouse management systems.
Distributors need to understand inventory and warehouse technologies so they can improve and automate business processes. They must understand how to utilize ERP and WMS features effectively for inventory management, order processing, inventory transactions, warehouse automation, and compliance and reporting.
A disciplined strategy is critical to the success of warehouse modernization projects. The strategy establishes a solid foundation, provides research, and defines priorities for the modernization plan. A four-phased execution approach ensures that distributors are prepared for implementations with continuous review and process improvement.
Acumatica Distribution Edition provides a modern platform for wholesalers to modernize warehouse operations with tools to manage projects, support cases, and installations or upgrades. Through leading-edge cloud technology, Acumatica Distribution Edition delivers unparalleled value to small and midmarket distributors. Integrated workflows span the full suite of business management applications with native warehouse management and barcoding features.
Comments